POWER GENERATION SYSTEMS THAT UTILIZE WASTE HEAT IN CEMENT PLANTS
FOREWORD
- To day, in the world, even if most advanced cement kiln system, highest efficiency, large amount of thermal energy from the pre-heater and clinker cooler emits to the environment.
- Can make use of this thermal energy to generate electricity.
- Depending on the kiln technology, the moisture of the input mill that the amount of heat utilized can vary. Overall, a power generation system utilizing waste heat can meet 30% power needs of the plant.
Benefits of power generation systems that utilize waste heat in cement plants, according to LBNL 2008, EPA 2010 reports:
- Reduce the amount of electricity purchased or reduce the dependence on self-generating power plants, reducing operating costs;
- Helps reduce pressure on electricity prices;
- Increase energy reliability for the plant;
- Increasing the competitive position of the factory in the market;
- Reduce energy consumption, reduce greenhouse gas emissions.
Overview about Power generation systems utilize waste heat
Power generation systems utilize waste heat in a cement plant operated on a Rankine cycle according to the basic working principle: the heat source (boiler) helps convert working chemicals from liquid to steam form temperature. high, high pressure; steam expands, generating the turbine turbine generator, then thanks to the condenser, the steam is condensed back to liquid form and returned to the boiler to continue the cycle.
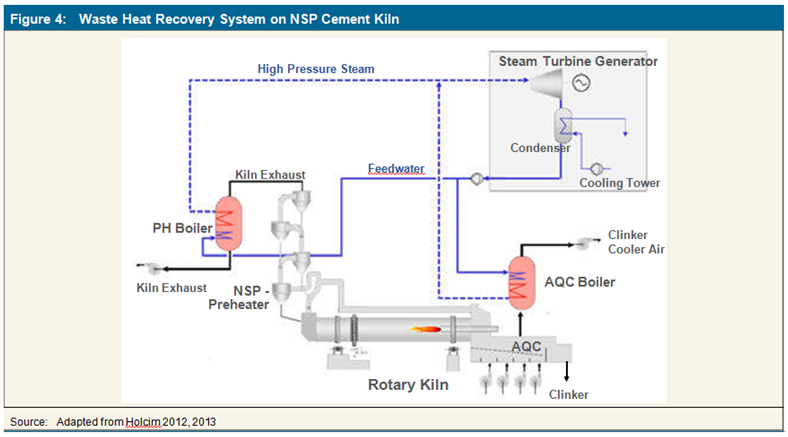
Technology diagram of a power generation system utilizing waste heat in cement plants
Classification of power generation systems utilizing waste heat
Based on working quality, power generation systems utilize waste heat currently divided into 3 main types as follows (according to Gibbon 2013, EPA 2012, CII 2009):
- Steam Rankine Cycle (SRC)
- Organic Rankine Cycle (ORC)
- The Kalina cycle uses a mixture of water and a new promoter
1. Steam Rankine Cycle – SRC
- The most widely used system to date for cement plants, with the following characteristics:
- The most familiar to the cement industry, generally suitable for conditions of heat sources higher than 300 ° C
- Based on proven technologies and simple operation
- Available with multiple supplier
- Installation cost by investment rate (US $ / kW) is lower than other systems
- A high-temperature waste heat source is required for optimal operation (minimum 260 ° C) - the generation of electricity efficiency will be significantly reduced if the temperature is lower, also when steam pressure and temperature are low can lead to partial condensation, eroding turbine blades.
- Typically, the waste heat from the clinker cooler is taken from the central wind of the cooler device to achieve an acceptable temperature for the system, but it means we have to accept some of the waste heat from the cooling equipment clinker will not be utilized.
- Full-time operating mode is required for this system, depending on local regulations.
- It is required to have a stable system of parameters of water supply.
- Condensers system are usually cooled by watet, wind-cooled condensers will affect system performance due to the need for deeper vacuum levels.
- This system is Good compatibility with high-capacity furnaces and low-humidity input furnaces (result is high exhaust temperature).
2. Organic Rankine Cycle - ORC
- Using work substances that are organic substances with large molecular weight such as butan, pentan.
- Low boiling point, high pressure steam
- Applicable to waste heat sources with a low temperature of about 150 oC (for steam systems, the minimum temperature must be 260 oC)
- Design with 2 levels of endothermic:
Level 1: Collects heat from the exhaust gas into the intermediate heat substances (eg heat conduction oil)
Level 2: Collect heat from intermediate heat substances into organic working substances
Some technical characteristics of ORC organic matter systems (according to Turboden 2012, Holcim 2011, Ormat 2012, Gibbon 2013):
- This system can take advantage of the heat source from the exhaust gas which has a lower temperature than the traditional steam system, which makes full use of the waste heat from the clinker cooler.
- The condenser operates at pressures above the atmospheric level, avoiding the risk of air entering the system resulting in complete removal of the air chasing device.
- The system operates with relatively low pressure, so it can be operated automatically.
- The working substance is always in a dry state, not partially condensed like steam, which helps prevent turbine wing form corrosion.
- Condensers device can be air-cooled without reducing system performance.
- The system uses ORC for the turbine blades to rotate at a slower speed, the generator motor can be directly connected without the gear box, avoiding reduction of transmission efficiency.
- The main equipment (turbines, pipes, condensers, heat exchanger surfaces) are smaller in size than steam systems. Turbines have fewer floors than steam systems.
- This system is Usually applies to sources of low temperature or limited size. The capacity of an ORC system is also usually smaller than steam system.
- Investment costs US $ / kW are higher than steam systems
- The two-stage thermal technology causes problems in the efficiency of the system.
- Intermediate heat and organics substances are flammable so protective devices are required and must be changed periodically. There are also potential risks to the environment in the case of system leaking.
- In general, the ORC system is suitable for small and medium-sized cement factory, high-efficiency furnaces or high-humidity input furnaces.
3. The Kalina cycle uses a mixture of water and amnonia
- The working substance is a mixture of 2 components: water and ammonia, which helps to increase the absorption heat efficiency.
- This system can Apply to waste heat source with low or fluctuating temperature.
- The system uses the Kalina cycle to have a very wide operating temperature range, which can receive heat sources from 95oC to 535oC.
- It is proved that 15% to 25% higher efficiency in ORC systems with the same temperature
Some technical characteristics of the system using Kalina cycle (according to Gibbon 2013, Mirolli 2012):
- Can be used for heat sources with lower temperatures than systems using conventional Steam Rankine cycles.
- This system has Highly flexible, the system has a large operating range and can respond quickly in the event of a change in the temperature and flow of the exhaust gas.
- The water and ammonia mixture can be adjusted to achieve high thermal conductivity and high efficiency in proportion to temperature and flue gas flow.
- The working solvent mixture is not flammable
- This is a new technology that is in the stage of introduction to the market, so it has limited manufacturers and experience
Compare 2 diagrams between Rankine cycle diagrams and Kalina cycle

Compiled by Cost Solutions Company Limited